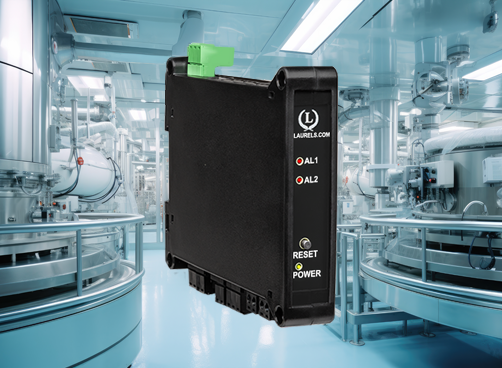
Features
- Reads 100Ω platinum, 10Ω copper & 120Ω nickel RTDs
- Accuracy ±0.01% of reading ±0.04°C (±0.07°F)
- 2, 3 or 4-wire connection with lead resistance compensation
- User selectable input span from entire RTD range down to 15.0°
- Selectable 1°, 0.1°, or 0.01° resolution, °C, °F, K or R
- All input ranges are user selectable and factory calibrated
- Up to 60 conversions per second, Ideal for peak or valley capture
- 4-20 mA, 0-20 mA, 0-10V or -10V to +10V transmitter output, (isolated)
- Analog output resolution 0.0015% of span, accuracy ±0.02% of span
- Ethernet data I/O, Modbus TCP
- Dual 120 mA solid state relays for alarm or control (isolated)
- Power 85-264 Vac / 90-300 Vdc or 10-48 Vdc / 12-32 Vac (isolated)
- DIN rail mount housing, 22.5 mm wide, detachable screw-clamp connectors
- Operating temperature from -40°C to 70°C (-40°F to 158°F)
The Laureate™ LTE Series DIN rail analog transmitter with ethernet communication and analog outputs for versatile connectivity.
The digitally programmable transmitter features two relays for alarm or control. The series offers exceptional accuracy of 0.01% of reading ± 2 counts, with high read rates at up to 60 or 50 conversions per second. The LTE Series transmitters offer the same high performance, signal conditioning, and programmable features as Laureate digital panel meters, counters, and timers.The Laureate 4-20 mA, 0-20 mA, 0-10V or -10V to +10V and ethernet output transmitter for RTD temperature offers the same high performance, signal conditioning and programmable features as Laureate digital panel meters, counters & timers provides six voltage input ranges and four current input ranges, all factory calibrated and jumper selectable. The temperature transmitter provides a linearized, highly accurate, stable and repeatable transmitter output for 100 ohm platinum, 10 ohm copper and 120 ohm nickel RTDs. Pt100 platinum RTDs can have a DIN alpha of 0.00385 or ANSI alpha of 0.00392. The RTD type and temperature range, specified in °C or °F, are user-selectable. The temperature range can be as wide as the entire span of the RTD type or as narrow as 150 counts (such as 15.0°), limited only by considerations of electrical noise and digital filtering time constants.
RTD connections can be via 2, 3 or 4 wires. With 3 or 4-wire connections, the transmitter automatically compensates for changes in lead resistance to the sensor. With 2-wire connection, the transmitter can measure and then subtract the lead wire resistance.
All RTD types are factory-calibrated, with calibration factors for each range securely stored in an onboard EEPROM. These factors can be scaled via software to accommodate external shunts, enabling field replacement of signal conditioner boards without necessitating recalibration of the associated transmitter. For optimal accuracy, factory recalibration is recommended annually. All Laurel Electronics instruments undergo factory calibration using the industry-leading Fluke calibrators, which are recalibrated yearly and certified traceable to national standards, ensuring the highest level of precision and reliability.
Calibration data is stored in EEPROM on the signal conditioner board. This allows signal conditioner boards and ranges to be changed in the field with no need for recalibration. Typical accuracy for a Pt100 is better than ±0.04°C (±0.07°F) ±0.01% of reading. Open sensor indication is standard and may be set up to indicate either upscale or downscale. RTD excitation is provided by the transmitter. RTD connections can be of the 2-, 3- or 4-wire type. With 3- and 4-wire connections, the transmitter automatically compensates for changes in lead resistance to the sensor. Instrument Setup Software allows user calibration for RTDs whose resistance is different than nominal at 0°C.
Laureate Transmitters are easily programmed with Laurel’s free Instrument Setup Software, downloadable from our website and compatible with Windows PCs, requiring a data interface board for setup.
High read rate of up to 50 or 60 conversions per second, the Laureate™ LTE Series transmitter uses Concurrent Slope (US Pat. 5,262,780) analog-to-digital conversion to integrate signals over a full power line cycle (50 Hz or 60 Hz). This read rate enables peak and valley capture, real-time computer interfacing, and control applications. Peak and valley values are automatically captured and can be viewed using Laurel’s free Instrument Setup Software (compatible with Windows PCs) or transmitted as serial data.
Standard Features of Laureate LTE Transmitters Include:
- Ethernet I/O, (isolated). The supported protocols are Modbus RTU and ASCII, which are tunneled via Modbus TCP. Note that RS232 or RS485 data I/O is provided by Laurel's LT Series transmitters.
- 4-20 mA, 0-20 mA or 0-10V analog transmitter output, (isolated), jumper-selectable and user scalable. All selections provide 16-bit (0.0015 ) resolution of output span and 0.02% output accuracy of a reading from -99,999 to +99,999 counts that is also transmitted digitally. Output isolation from signal and power grounds eliminates potential ground loop problems. The supply can drive 20 mA into a 500 ohm (or lower) load for 10V compliance, or 10V into a 5K ohm (or higher) load for 2 mA compliance.
- Dual solid state relays, (isolated). Available for local alarm or control. Rated 120 mA at 130 Vac or 180 Vdc.
- Selectable transducer excitation output, (isolated), user selectable 5V@100 mA, 10V@120 mA, 12V@100 mA, or 24V@50 mA.
- Power 85-264 Vac, (isolated), low-voltage 10-48 Vdc or 12-32 Vac power is optional.
Digital signal filtering modes can be selected to ensure stable readings in electrically noisy environments.
- An unfiltered selection provides true peak and valley readings and aids in control applications.
- A batch average filter selection averages each 16 conversions.
- Dual solid state relays for control or alarm, (isolated). Rated 120 mA at 140 Vac or 180 Vdc. The relays can respond to digital readings or to received control characters.
- An adaptive moving average filter selection provides a choice of 8 time constants from 80 ms to 9.6 s. When a significant change in signal level occurs, the filter adapts by briefly switching to the shortest time to follow the change, then reverts back to its selected time constant. An auto setting selects the time constant selection based on signal noise.
Two tare functions: auto-tare and manual tare. In auto-tare, an input line is grounded by an external pushbutton. This causes the current weight, which is normally the empty weight of the container to be stored in memory as an offset. In manual tare, the tare value can be entered manually via a control input pushbutton or using Laurel's free Instrument Setup Software.
Peak and valley values are automatically captured. These may be displayed via Laurel's free Instrument Setup Software, which runs on a PC under MS Windows or can be transmitted as serial data.
LTE series DIN rail transmitters & signal conditioners can be interfaced to a wide range of sensors and transducers using one of seven available plug-in signal conditioner boards. The transmitters duplicate the high performance (high accuracy, high read rate) and extensive programmable features of Laureate 1/8 DIN digital panel meters, counters and timers. They utilize the same signal conditioners boards, much of the same firmware, and Laurel's free Windows-based Instrument Setup Software. They come in a compact DIN rail mount package with detachable screw-clamp connectors for easy wiring.
The LTE series Transmitters accessible from this page include a 4-20 mA, 0-20 mA, 0-10V, or -10V to +10V analog output (isolated, user selectable), an ethernet serial data interface (isolated, user selectable), and dual 120 mA solid state AC/DC relays (isolated). An (isolated) 5, 10, 12, or 24 Vdc transducer excitation output is included with all models other than those with a temperature or AC RMS signal conditioner.
Connecting Laureate LTE Transmitters to a Local Area Network (LAN)
Laurel LTE series Ethernet transmitters can connect directly to a LAN via an Ethernet cable. Up to 30 Laureate LT Transmitters and/or Digital Panel Meters can be configured for RS485 and daisy-chained to an LT Transmitter for seamless LAN integration. Setup for both configurations is streamlined using Laurel’s free Instrument Setup Software, which simplifies node discovery and transmitter configuration.
Flexible Communication Options for LTE Transmitters
Laureate Transmitters can be equipped with Laurel communication boards to support various interfaces and protocols. These include serial interfaces with ASCII or Modbus RTU protocols, and Ethernet interfaces with web access, ASCII, or Modbus TCP/IP protocols, ensuring versatile connectivity for your commercial applications.
LTE Transmitter Signal Input & Function | Model Series | Analog Output | Ethernet I/O | Dual Relays | |
---|---|---|---|---|---|
1 | DC Input Voltage and Current | LTE-DC | ![]() |
![]() |
![]() |
2 | AC RMS Voltage or Current | LTE-RMS | ![]() |
![]() |
![]() |
3 | Process Voltage or Current | LTE-P | ![]() |
![]() |
![]() |
4 | Strain Gauge or Potentiometer Follower | LTE-SG | ![]() |
![]() |
![]() |
5 | Weighing Applications | LTE-WA | ![]() |
![]() |
![]() |
6 | Load Cell & Microvolt Signals | LTE-WM | ![]() |
![]() |
![]() |
7 | Thermocouple (Types J, K, T, E, N, R, S) | LTE-TC | ![]() |
![]() |
![]() |
8 | RTD Temperature | LTE-RTD | ![]() |
![]() |
![]() |
9 | Resistance in Ohms | LTE-R | ![]() |
![]() |
![]() |
10 | Frequency, Rate, Speed | LTE-FR | ![]() |
![]() |
![]() |
11 | Pulse Input Totalizer | LTE-FR | ![]() |
![]() |
![]() |
12 | Process Signal Totalizer | LTE-VF | ![]() |
![]() |
![]() |
13 | Batch Controller Analog Input | LTE-FR | ![]() |
![]() |
![]() |
14 | Batch Controller Pulse Input | LTE-FR | ![]() |
![]() |
![]() |
15 | Sum, Difference, Ratio, Product of 2 Inputs | LTE-FR | ![]() |
![]() |
![]() |
16 | On/Off Duty Cycle | LTE-FR | ![]() |
![]() |
![]() |
17 | Stopwatch Timing for Single Events | LTE-FR | ![]() |
![]() |
![]() |
18 | Average Time of Periodic Events | LTE-FR | ![]() |
![]() |
![]() |
19 | AC Phase Angle and Power Factor | LTE-FR | ![]() |
![]() |
![]() |
20 | Quadrature Position or Rate | LTE-QD | ![]() |
![]() |
![]() |
Laureate Ethernet & 4-20 mA Output Thermocouple Temperature Transmitter
RTD Metal | Alpha | R at 0°C | R at top of range |
Excitation Current |
Range | Max Error |
---|---|---|---|---|---|---|
Platinum Pt100 |
0.003850 (DIN) | 100Ω | 390.48Ω at 850°C |
196 µA | -202°C to +850°C -331°F to +1562°F |
±0.03°C ±0.01% of rdg ±0.05°F ±0.01% of rdg |
Platinum Pt100 |
0.003902 (ANSI) | 100Ω | 394.36Ω at 850°C |
196 µA | -202°C to +850°C -331°F to +1168°F |
±0.04°C ±0.01% of rdg ±0.07°F ±0.01% of rdg |
Nickel Ni120 |
0.00672 | 120Ω | 380.31Ω at 260°C |
196 µA | -80°C to +260°C -112°F to +500°F |
±0.05°C ±0.01% of rdg ±0.09°F ±0.01% of rdg |
Copper Cu10 |
0.00427 | 9.035Ω | 19.116Ω at 260°C |
5.0 mA | -100°C to +260°C -148°F to +500°F |
±0.05°C ±0.01% of rdg ±0.09°F ±0.01% of rdg |
Recalibration: All ranges are calibrated at the factory. Recalibration is recommended every 12 months. |
RTD Input | ||||
---|---|---|---|---|
Calibration, Pt 100 DIN | IEC 751 (IPTS-68) | |||
Calibration, Pt 100 ANSI | NIST Monograph 126 | |||
Configuration | 2, 3 or 4-wire connection | |||
Excitation current | 0.2 mA | |||
Max error at 25°C, Pt100 | ±0.04°C (±0.07°F) ±0.01% of reading | |||
Span tempco | ±0.003% of reading/°C | |||
Zero tempco | ±0.03 deg/deg | |||
Sensor lead resistance | 2-wire: 10 mdeg/Ω/deg up to 10Ω; | |||
tempco per conductor | 3 & 4-wire: 10 μdeg/Ω/deg up to 100Ω | |||
Over-voltage protection | 125 Vac | |||
Open sensor indication | 0 mA or > 20 mA output, selectable | |||
Provision for user calibration | Multiplier of RTD resistance plus offset in degrees | |||
Analog Output (standard) | ||||
Output Levels | 4-20 mA and 0-10 Vdc (selectable) | |||
Compliance, 4-20 mA | 10V (0-500Ω load) | |||
Compliance, 0-10V | 2 mA (5 kΩ load) | |||
Output Resolution | 16 bits (65,536 steps) | |||
Output Accuracy | ±0.02% of output span | |||
Output Isolation | 250V rms working, 2.3 kV rms per 1 minute test | |||
Step response time | 50 ms | |||
Ethernet Data I/O (standard) | ||||
Type | 10/100Base-T Ethernet per IEEE 802.3 | |||
Data Rates | 300, 600, 1200, 2400, 4800, 9600, 19200 baud | |||
Output Isolation | 250V rms working, 2.3 kV rms per 1 min test | |||
Serial Protocol | Modbus TCP | |||
Modbus Compliance | Modbus over Serial Line Specification V1.0 (2002) | |||
Digital Addresses | 247 for Modbus | |||
Dual Relay Output (standard) | ||||
Relay Type | Two solid state relays, SPST, normally open, Form A | |||
Load Rating | 120 mA at 140 Vac or 180 Vdc | |||
Power Input | ||||
Standard Power | 85-264 Vac or 90-300 Vdc | |||
Low Power Option | 10-48 Vdc or 12-32 Vac | |||
Power Frequency | DC or 47-63 Hz | |||
Power Isolation | 250V rms working, 2.3 kV rms per 1 min test | |||
Power Consumption | 2.5W typical at 24V | |||
Environmental | ||||
Operating Temperature | -40°C to 70°C (-40°F to 158°F) | |||
Storage Temperature | -40°C to 85°C (-40°F to 185°F) | |||
Relative Humidity | 95% at 40°C, non-condensing | |||
Cooling Required | Mount transmitters with ventilation holes at top and bottom. Leave 6 mm (1/4") between transmitters, or force air with a fan. | |||
Mechanical | ||||
Enclosure | Rugged black polycarbonate housing material | |||
Mounting | 35 mm rail per DIN EN 50022 | |||
Dimensions | 129 x 104 x 22.5 mm case | |||
Connectors | Detachable screw clamp connectors meet VDE / IEC / UL / CSA standards. RJ45 jack for Ethernet | |||
Tightening Torque | Screw terminal connectors: 5 lb-in (0.56 Nm) | |||
Weight | Complete transmitter: 183 g (6.5 oz) | |||
General | ||||
Programming | Utilize Laurel's free Instrument Setup Software, which runs on a PC under MS Windows. | |||
Security | Lockout options available using Laurel's free Instrument Setup Software. | |||
Warranty | 3 years parts & labor | |||
Recalibration: All ranges are calibrated at the factory. Recalibration is recommended every 12 months. |
Transmitter Pinout
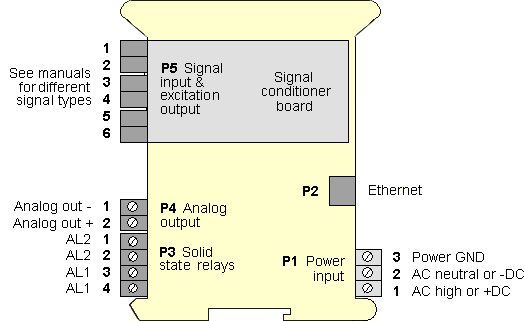
RTD hookup can be via 2, 3 or 4 wires to the J5 connector. The transmitter applies an excitation current of 196 µA (Pt 100 and Ni 120) or 5 mA (Cu 10).
![]() |
In 4-wire hookup, different pairs of leads are used to apply the excitation current and sense the voltage drop across the RTD, so that the IR drop across the excitation leads is not a factor. |
![]() |
In 3-wire hookup, the transmitter senses the combined voltage drop across the RTD plus two excitation leads. It also senses the voltage drop across one excitation lead, and then subtracts twice this voltage from the combined total. This technique effectively subtracts all lead resistance and compensates for ambient temperature changes if the two excitation leads are identical. |
![]() |
In 2-wire hookup, the transmitter senses the combined voltage drop across the RTD and both lead wires. The voltage drop across the lead wires can be measured by shorting out the RTD during transmitter setup, and this voltage is then automatically subtracted from the combined total. However, changing resistance of the lead wires due to ambient temperature changes will not be compensated. |
Free Instrument Setup Software for Series 2 Laureates
Free Downloadable Windows-based Instrument Setup (IS) software (Data Interface Board Required) for use with our programmable Digital Panel Meters, Scale Meters, Counters, Timers, Remote Displays, and Transmitters, are an easy method to set up Laureate 1/8 DIN digital panel meters, counters, timers, remote displays, and DIN-rail transmitters, as explained in the Instrument Setup Software Manual. Laureate 1/8 DIN instruments can also be set up from the front panel, as explained in their respective Owners Manuals. Instrument Setup software is of benefit whether or not the PC is connected to the instrument.
- When the PC is connected to the instrument, Instrument Setup software can retrieve the setup file from the instrument or open a default setup file or previously saved setup file from disk View Setup, then provides graphical user interface (GUI) screens with pull-down menus applicable to input, display, scaling, filtering, alarms, communications, analog output, and front panel lockouts. Fields that are not applicable to the instrument as configured are either left out or grayed out. Clicking on any item will bring up a detailed Help screen for that item. After editing, the setup file can be downloaded, uploaded to the instrument, or saved to a disk. The same setup file can then be downloaded into multiple instruments.
- When the PC is not connected to the instrument, the above GUI screens can be used to set up a virtual instrument. The setup file can then be saved to disk. Switching toView Menu then brings up a screen with the required front panel programming steps. This view can be printed out for use at the instrument site and to serve as a hard copy record.
Download Free Instrument Setup Software
Installation
Set User Account Control (UAC) of MS Windows to "Never notifiy me" so that Instrument Setup Software can create directories. The UAC change screen can be reached as follows:
- Under Windows 7, click on the Windows Start button in the lower left of the desktop and enter "UAC" in the search field.
- Under Windows 8, navigate to Control Panel, then to the "User Accounts and Family Safety" section, and click on "Change User Account Control Settings."
- Under Windows 10, click on the Windows Start button in the lower left of the desktop, then on "Settings", and enter "UAC" in the search field.
- Reboot your computer for the changed UAC setting to take effect.
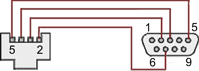
RJ11-to-DB9 cable with rear view of DB9 connector to PC
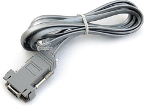
RS232 cable, meter to PC, P/N CBL01
Laureate 1/8 DIN Laureate instruments must be equipped with a serial communications board and be connected to the computer via a serial communications cable. The connection can be via RS232, RS485, USB or Ethernet. Following setup, the serial communications board may be removed from the instrument if desired. The wiring of the RS232 cable is illustrated above with end views of the two connectors.
Laureate LT Series transmitters come standard with a 3-wire serial interface, which can be jumpered for RS232 or RS485.
Laureate LTE Series transmitters come standard with an Ethernet interface.
Meter Setup Screens
Click on any of the reduced screens below for a full-size screen view, then click on the Back button of your browser to return to this page. The screens examples below are for a fully-loaded Series 2 Digital Panel Meter (DPM), which is connected to the PC via RS232. If the meter is a Series 1 meter (pre-2007), this is sensed by the software, and somewhat different screens are brought up. Please see Series 1 setup screens.











Meter Setup Utilities




From the Main Menu, click on Readings if your PC is connected to the meter. A pull-down menu then offers three choices: List, Plot and Graph.
- List presents the latest readings in a 20-row by 10-column table. Press Pause at any time to freeze the display. This is one method to capture peak readings.
- Plot generates a plot of readings vs. time in seconds. It effectively turns the DPM-PC combination into a printing digital oscilloscope.
- Graph generates a histogram where the horizontal axis is the reading and the vertical axis is the number of occurrences of readings. The display continually resizes itself as the number of readings increases.


Dimensions
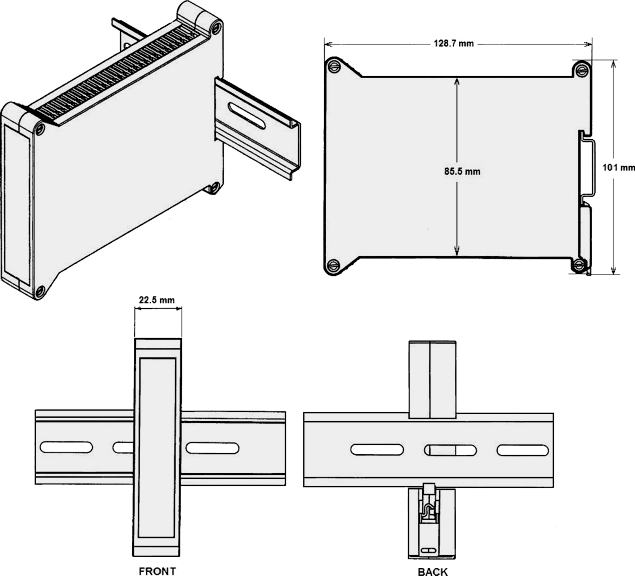
Dimensioned CAD assembly drawings in EPRT, STEP, x_t, .dwg, pdf file formats: Laureate-transmitter-case.zip (zipping prevents browser from opening CAD files as text files).
CBL02
USB-to-RS232 Adapter Cable
CBL04
RS232 Cable for LT Transmitters
Understanding the LTE DIN Rail Analog Transmitter with Ethernet Communication and Analog Outputs for RTD Temperature
In the realm of industrial automation and control, precision and reliability are paramount. The LTE Series DIN Rail Analog Transmitter with Ethernet Communication and Analog Outputs for RTD Temperature stands out as a robust solution designed to meet these demands. This article will explore what makes this device essential in temperature measurement and control systems, its features, and its benefits.
What is an LTE Series DIN Rail Analog Transmitter?
The LTE Series DIN Rail Analog Transmitter is a specialized device designed to convert temperature readings from Resistance Temperature Detectors (RTDs) into analog signals and communicate data over Ethernet. It is designed to be mounted on DIN rails, which are standard mounting components in control panels and industrial settings, providing a compact and organized installation.
Key Features
- RTD Temperature Measurement:
- RTD (Resistance Temperature Detector): RTDs are sensors used for precise temperature measurements. They work on the principle that the electrical resistance of a metal increases with temperature. The LTE Series transmitter reads this resistance and converts it into a readable temperature value.
- Analog Outputs:
- The transmitter provides analog outputs, typically in 4-20 mA or 0-10 V formats, which can be easily integrated into existing analog systems for monitoring and control.
- Ethernet Communication:
- Network Integration: The device features Ethernet communication capabilities, allowing it to transmit data over a network. This integration supports remote monitoring and control, enhancing system flexibility and data accessibility.
- Protocols and Configuration: The Ethernet interface usually supports standard communication protocols like Modbus TCP/IP or others, making it compatible with various industrial control systems.
- DIN Rail Mounting:
- The device is designed to be mounted on DIN rails, facilitating straightforward installation and integration within control cabinets and industrial panels. This mounting method ensures durability and stability in a variety of operating environments.
- High Accuracy and Stability:
- Precision Measurement: The LTE Series transmitter is engineered to deliver accurate and stable temperature readings, ensuring reliable performance in critical applications.
Applications
- Industrial Automation:
- In industrial processes where temperature control is crucial, the LTE Series transmitter ensures accurate temperature measurement and reliable signal transmission to control systems.
- Building Management Systems:
- For HVAC systems and building automation, accurate temperature data is essential for efficient operation. The transmitter’s Ethernet communication capabilities enable seamless integration with building management systems.
- Manufacturing Processes:
- In manufacturing, precise temperature control is vital for product quality. The LTE Series transmitter helps maintain the desired temperature conditions by providing real-time data to control systems.
Benefits
- Enhanced Monitoring and Control:
- The combination of analog outputs and Ethernet communication allows for both local and remote monitoring and control, providing flexibility in managing temperature-sensitive processes.
- Improved Data Accuracy:
- The transmitter’s high accuracy ensures reliable temperature readings, which is crucial for maintaining quality and operational efficiency.
- Ease of Integration:
- The device’s compatibility with existing systems, through analog and Ethernet interfaces, simplifies integration and reduces setup time.
- Robust Construction:
- Designed for industrial environments, the LTE Series transmitter offers durability and reliability, making it suitable for a wide range of applications.
Conclusion
The LTE Series DIN Rail Analog Transmitter with Ethernet Communication and Analog Outputs for RTD Temperature represents a powerful tool in industrial temperature measurement and control. Its combination of precise RTD temperature measurement, analog output capabilities, and Ethernet communication makes it a versatile solution for a variety of applications. By providing accurate data and facilitating easy integration into existing systems, this device plays a crucial role in enhancing operational efficiency and ensuring quality in industrial processes.
Applications of LTE DIN Rail Analog Transmitter with Ethernet Communication and Analog Outputs for RTD Temperature
The LTE Series DIN Rail Analog Transmitter with Ethernet Communication and Analog Outputs for RTD (Resistance Temperature Detector) Temperature offers a versatile solution to meet these needs. Here’s an overview of where this advanced device is typically used and how it benefits various applications.
1. Industrial Manufacturing
In industrial manufacturing environments, temperature control is crucial for maintaining product quality and operational efficiency. The LTE Series transmitter allows for accurate temperature measurement of processes such as extrusion, molding, and heating. By integrating with Ethernet networks, the device enables real-time data monitoring and control, which is essential for ensuring consistent production standards and early detection of process deviations.
2. Building Management Systems (BMS)
Building Management Systems utilize temperature sensors to manage HVAC (Heating, Ventilation, and Air Conditioning) systems effectively. The LTE Series transmitter is employed to monitor and control the temperature within buildings, ensuring energy efficiency and comfort. Its ability to provide analog outputs and Ethernet communication makes it a valuable component for integrating temperature data into a BMS for optimized building climate control.
3. Energy Management
Energy management systems benefit from accurate temperature data for monitoring energy consumption and improving efficiency. The LTE Series transmitter can be used in power plants, substations, and renewable energy facilities to measure and monitor temperature at critical points. This helps in preventing overheating, optimizing energy use, and ensuring the safe operation of equipment.
4. Process Automation
In process automation, maintaining precise temperature control is essential for process stability and product quality. The LTE Series transmitter can be deployed in various processes such as chemical reactions, fermentation, and distillation. Its real-time Ethernet communication allows for seamless integration with process control systems, providing immediate feedback and control to maintain optimal conditions.
5. Environmental Monitoring
Environmental monitoring systems use temperature sensors to track climatic conditions and ensure compliance with environmental regulations. The LTE Series transmitter is used in applications such as weather stations and environmental control systems to measure and report temperature data. Its Ethernet capability facilitates remote monitoring and data analysis, enhancing the efficiency of environmental management practices.
6. Food and Beverage Industry
Temperature control is crucial in the food and beverage industry to ensure product safety and quality. The LTE Series transmitter is used to monitor temperatures in processes like cooking, cooling, and storage. By integrating with Ethernet networks, it provides real-time data for quality assurance and regulatory compliance, helping prevent spoilage and ensuring food safety.
7. Pharmaceutical Industry
In the pharmaceutical industry, precise temperature control is necessary for the production and storage of sensitive products. The LTE Series transmitter helps maintain and monitor temperatures in processes such as drug manufacturing and storage. Its ability to communicate via Ethernet ensures that temperature data can be easily integrated into quality control systems and compliance records.
Conclusion
The LTE Series DIN Rail Analog Transmitter with Ethernet Communication and Analog Outputs for RTD Temperature is a versatile tool across various industries. Its combination of accurate temperature measurement, Ethernet communication, and analog output capabilities makes it ideal for applications in industrial manufacturing, building management, energy management, process automation, environmental monitoring, food and beverage, and pharmaceuticals. By integrating this transmitter into their systems, industries can achieve improved process control, enhanced data accessibility, and overall operational efficiency.
Less Information.